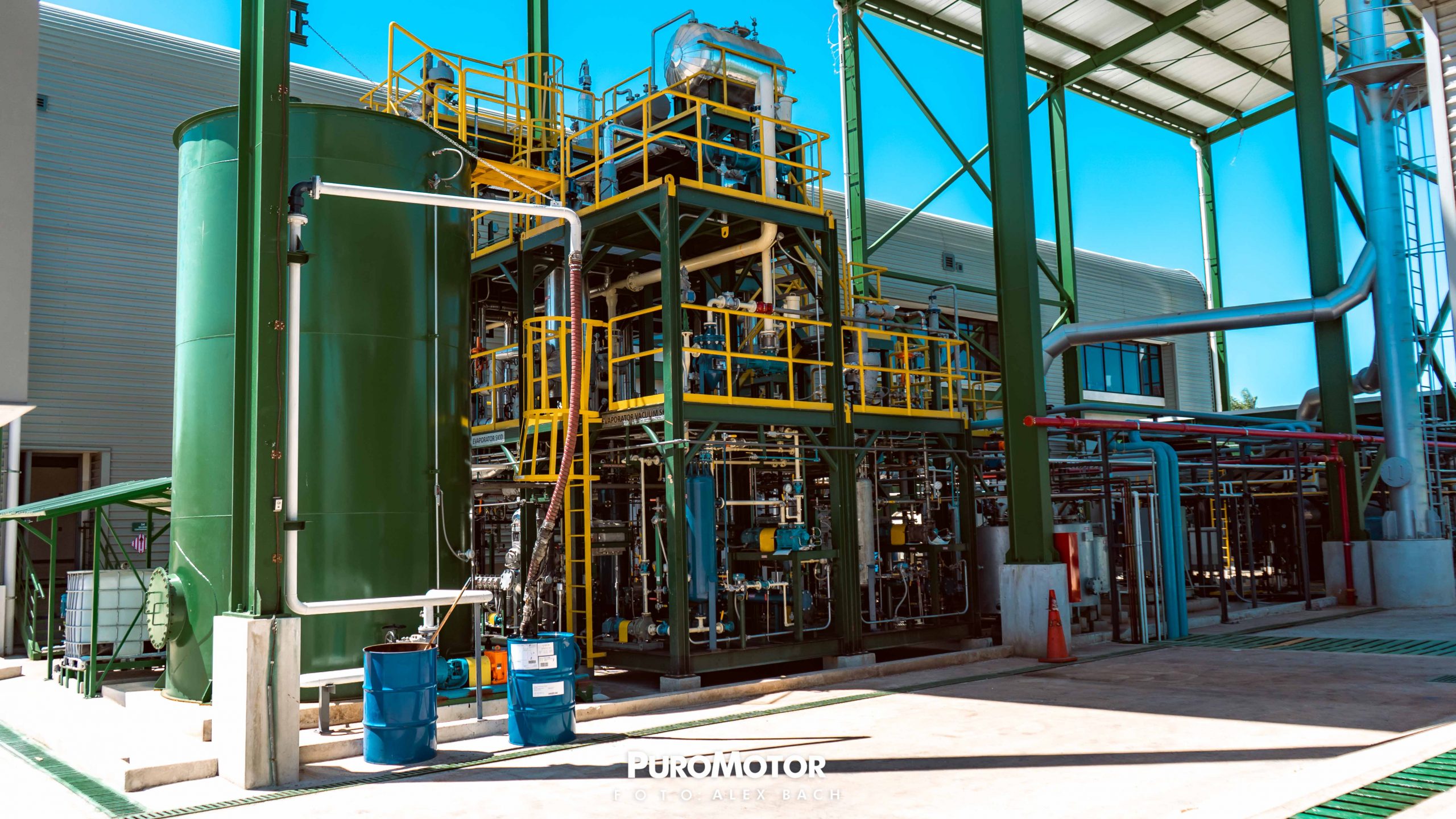
Probablemente, el nombre Metalub le sea familiar. Desde el 2015, la empresa incursionó en el mercado costarricense con el objetivo de impactar positivamente en el proceso de los lubricantes usados.
Inicialmente, la compañía recolectaba el aceite usado por los vehículos, lo enviaba a Estados Unidos para su re-refinamiento, y luego el lubricante regresaba a Costa Rica para ser utilizado nuevamente.
La empresa fue creciendo y este 2024 inauguró la primera planta re-refinadora de lubricantes en Centroamérica, reforzando así su compromiso con la economía circular de los aceites minerales usados. Esta planta, ubicada en Orotina, realiza todo el proceso que anteriormente se hacía en Estados Unicos, utilizando mano de obra costarricense y manteniendo todos los estándares de calidad que garantizan el producto.
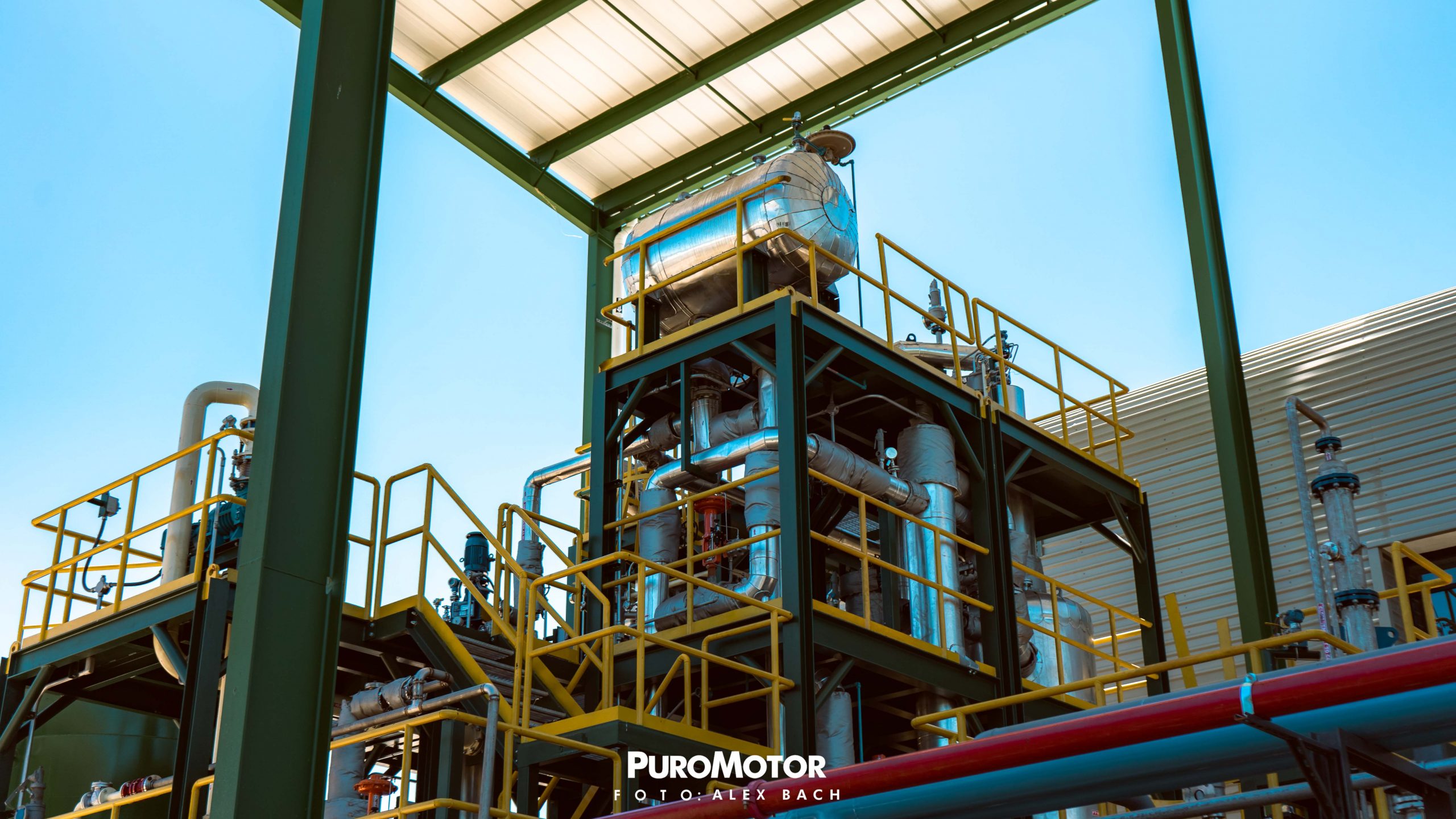
La operación de la plata de Metalub permite recuperar un promedio de 6 millones de litros de aceite usado al año y mitigar 15.000 toneladas de emisiones de carbono anualmente.
Es importante destacar que no todo el aceite usado se puede recibir, si tiene más de un 5% de agua no se puede re-refinar. Es por ello que Metalub ha realizado un trabajo continuo con los talleres y centros de acopio para darle al aceite usado un adecuado proceso.
Puro Motor visitó la planta para conocer el proceso que permite recuperar el aceite base de lubricantes usados, que, de lo contrario, serían desechados sin un tratamiento adecuado, contaminando la naturaleza.
¿Cómo se hace?
Metalub recolecta el aceite mineral usado de las empresas con flotas (camiones, tractores, autobuses, automóviles, taxis), empresas que suministran cambios de aceite (gasolineras, talleres mecánicos, lubricentros, concesionarias), y de sus propios Meta Centros, que ubicados en Walmart Escazú, Guadalupe y Cartago.
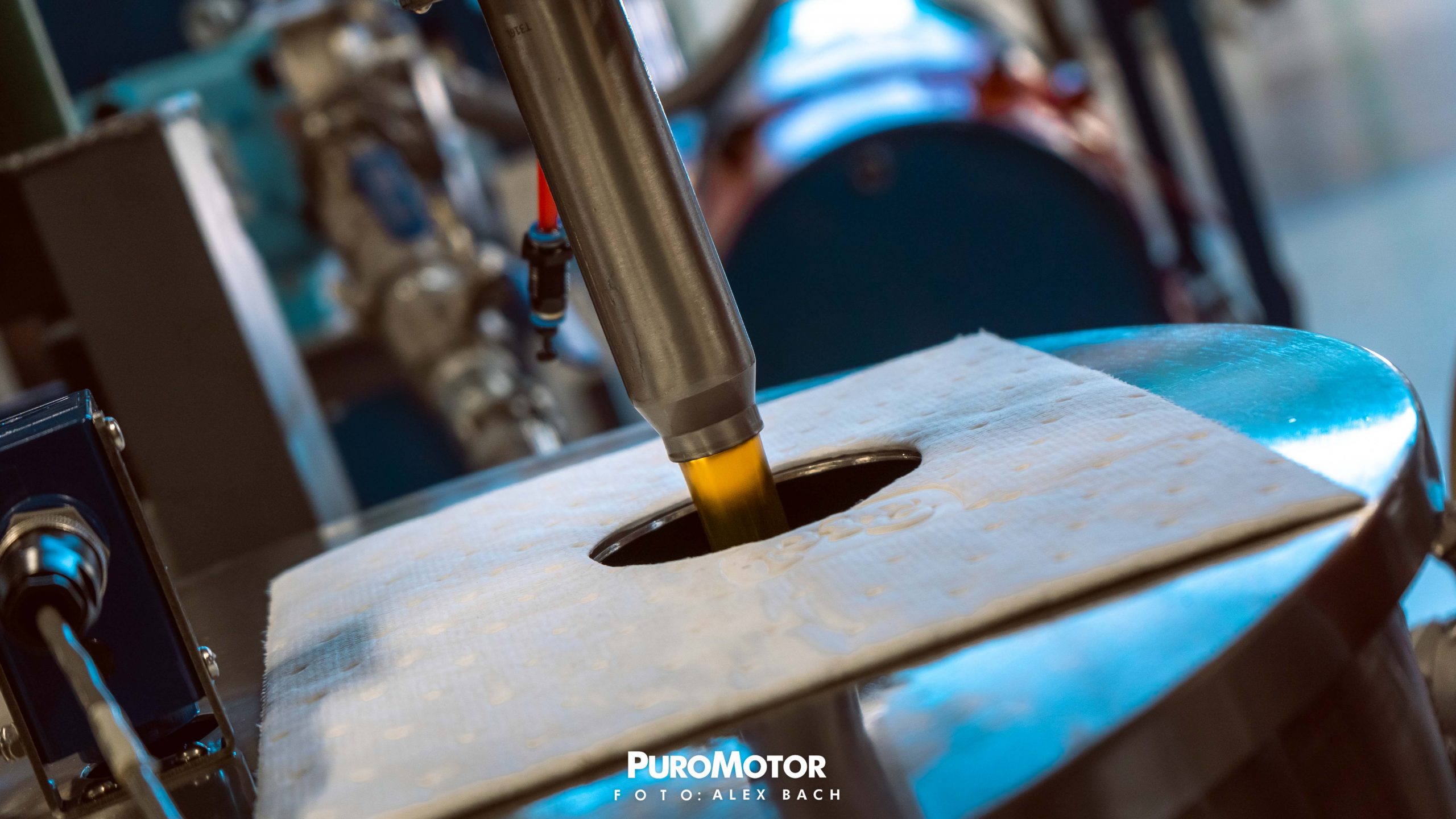
El aceite se recibe, se depura y se envía al módulo de refinación, donde a través de calor se separa el combustible del agua, posteriormente se destila para quitar la viscosidad de los aceites mezclados y el tercer paso es la extracción, donde se eliminan las impurezas.
Luego de estos pasos se recuperan diferentes subproductos: el primero y más importante es el aceite base para volver a generar lubricantes, de esta base se producen dos, una más viscosa que otra. El segundo subproducto que sale del aceite usado es asfalto, que posteriormente se utiliza en la construcción de carreteras y el tercero es diesel y gasolina que se utilizan en el mismo funcionamiento de la planta. De un lote de lubricante que se envía al módulo de refinación, entre un 75% y 80% se recupera para aceite base, el resto se divide en los subproductos.
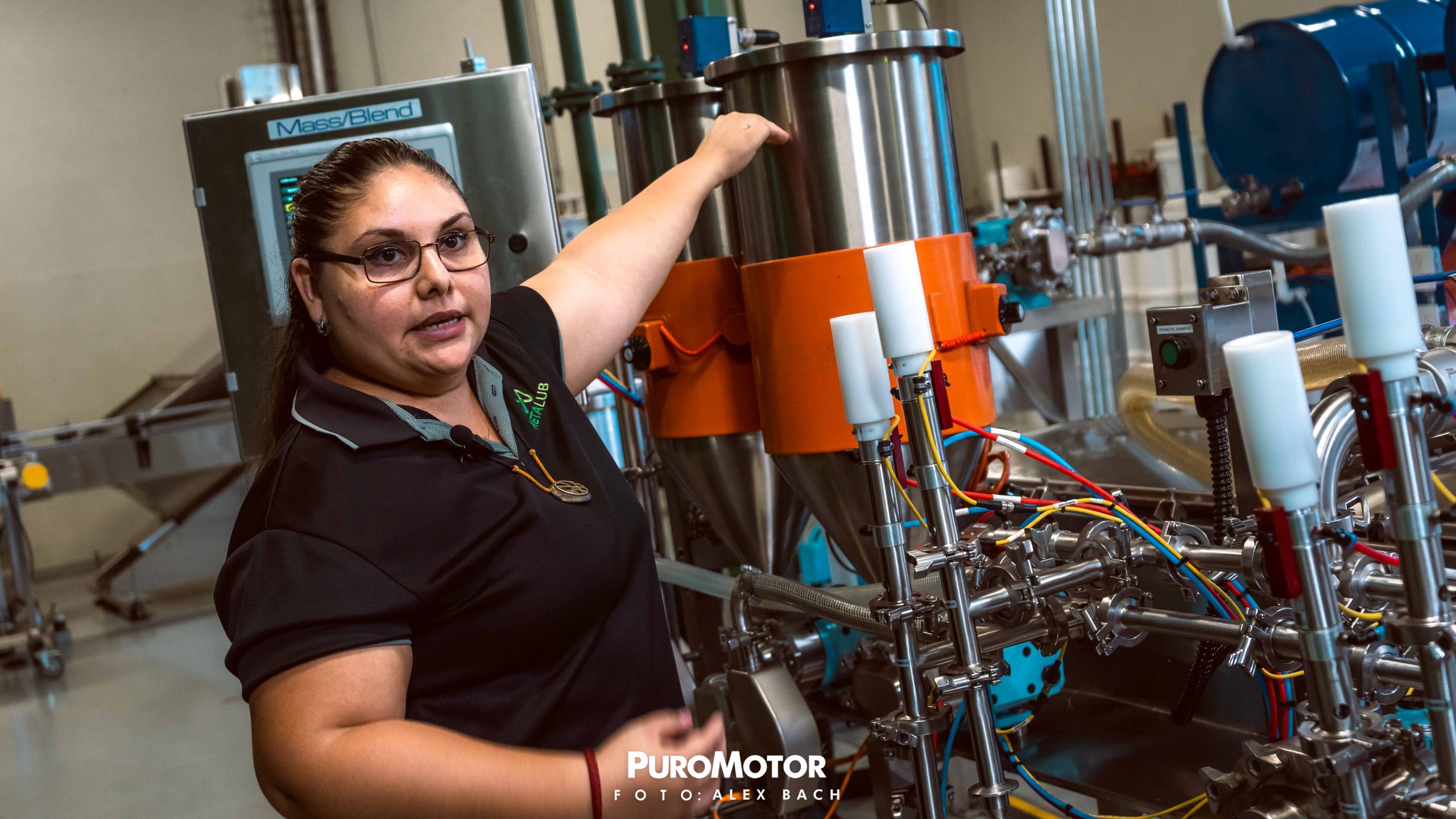
Una vez que se tiene el aceite base completamente limpio y transparente se envía por medio de tuberías al área de mezclado, ahí se divide de acuerdo a la viscosidad (pesado o liviano) según las regulaciones de API (American Petroleum Institute).
El siguiente paso es agregar los aditivos al aceite base a través de un sistema automatizado. Estos aditivos son formulados por el líder mundial en ese campo, Afton Chemicals, y son los encargados de darle las características de protección, lubricidad y detergencia a los nuevos lubricantes.
Una vez mezclado el aceite base con los aditivos, los diferentes tipos de aceites (según su tipo y viscosidad) son empacados en estañones, cubetas y cuartos y ya están listos para ser distribuidos en los puntos de ventas. Por día, en un turno de ocho horas, en la planta se producen entre 30 y 35 estañones de lubricantes.
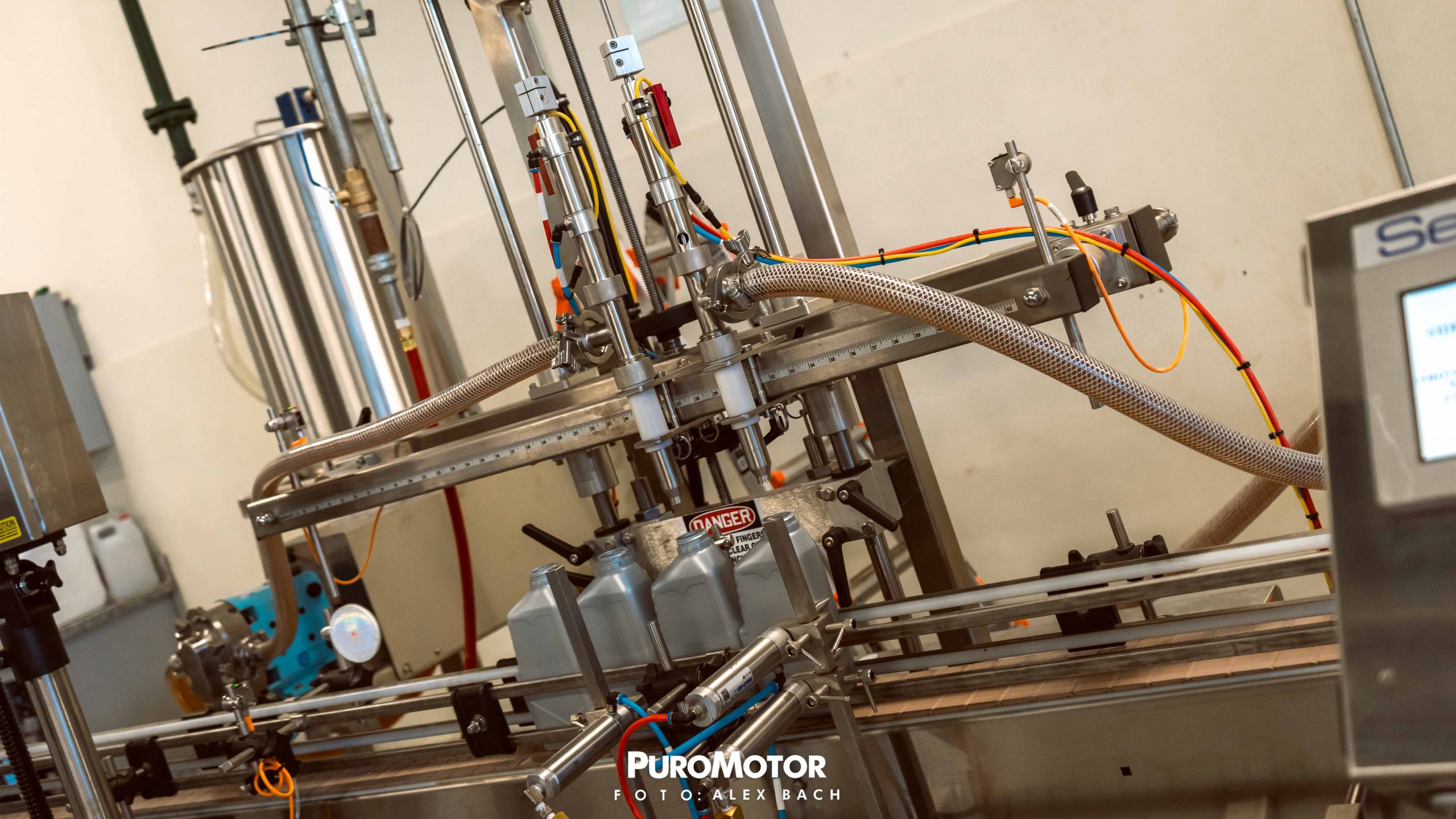
Cabe destacar que la planta de Metalub cuenta con un laboratorio con equipos de última tecnología que les permite analizar las muestras y garantizar la calidad de los lubricantes. De hecho, cumplen con los más altos estándares de la industria API (American Petroleum Institute) y están certificados por varios fabricantes de motores como Cummins, Detroit Diesel, Mack, Volvo, Renault, entre otros.
Un dato revelador es que de los lubricantes que se desechan en Costa Rica, Metalub recupera un máximo de un 10%, eso indica que un altísimo porcentaje se desecha sin un adecuado tratamiento en el país.